What is Silicone Injection Molding
Silicone injection molding is an advanced manufacturing process that involves injecting liquid silicone rubber (LSR) into a precisely designed mold cavity to produce silicone components. This technique is renowned for its efficiency and capability to manufacture complex, detailed parts with consistent quality. Key advantages of silicone injection molding include exceptional precision, fast production cycles, and the ability to create components with superior thermal and chemical resistance.
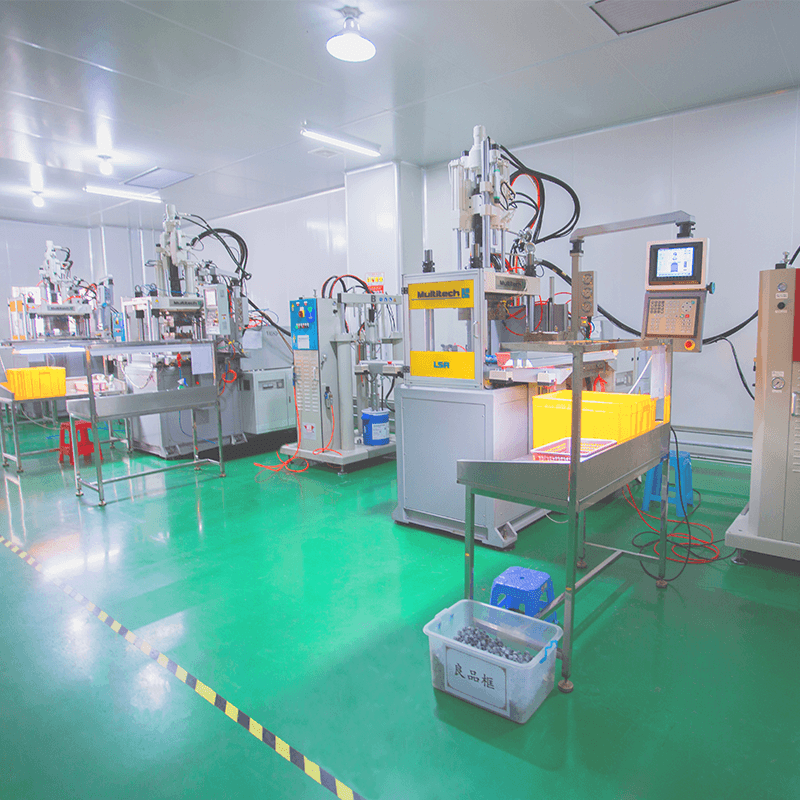
Silicone Injection Molding Process
The silicone injection molding process involves several key stages:
1. Material Preparation: The process begins with preparing the liquid silicone rubber (LSR), which consists of a base and a curing agent. These components are precisely mixed to achieve consistent material properties. The prepared LSR is then fed into the injection molding machine.
2. Mold Design: The mold, typically made from steel or aluminum, plays a critical role in shaping the final product. It consists of two parts: the cavity, which holds the silicone, and the core, which forms the interior surface of the product.
3. Injection: The mixed LSR is injected into the mold cavity under high pressure. This step is meticulously controlled to ensure the silicone fills the mold evenly and completely. Parameters such as injection pressure and speed are optimized to prevent defects like air bubbles or incomplete filling.
4. Curing: After injection, the silicone is cured by heating the mold to a specific temperature. This process initiates a cross-linking reaction that transforms the liquid silicone into a solid, rubber-like material. The curing time and temperature are precisely regulated to achieve the desired material properties.
5. Demolding: Once curing is complete, the mold is opened, and the finished silicone part is extracted. The part is inspected for quality, and any excess material, or flash, is trimmed off. The mold is then prepared for the next cycle.
6. Post-Curing: A post-curing step may be employed in certain applications, such as medical or food-grade products. This involves heating the parts in an oven at elevated temperatures for an extended period to enhance their properties further and meet stringent regulatory standards.
Advantages of the Silicone Injection Molding Process
1. High Precision and Consistency
Silicone injection molding excels in producing complex components with exceptional precision and consistency. The process allows for stringent control over injection parameters and mold design, resulting in products with minimal tolerances. This high level of accuracy is crucial for applications demanding precise dimensions and intricate geometries, such as medical devices and electronic components.
2. High Efficiency and Rapid Production Cycles
Silicone injection molding offers significantly shorter production cycles compared to traditional compression molding or casting. The high degree of automation in this process streamlines the production sequence—from raw material to finished product—allowing for rapid completion and large-volume production. This efficiency reduces the cost per unit and accelerates time-to-market.
3. Superior Material Properties
Silicone materials are renowned for their excellent properties, including resistance to extreme temperatures, chemical stability, and electrical insulation. The injection molding process capitalizes on these attributes, producing durable and versatile components. Additionally, silicone materials used in this process comply with FDA and LFGB standards, making them suitable for food-grade and medical applications.
4. Capability to Produce Complex Shapes
Silicone injection molding stands out for its ability to create intricate shapes and fine details. The superior flow characteristics of silicone allow for thorough mold filling, enabling the production of components with complex geometries, such as seals, keypad covers, and specialized medical devices.
5. Reduced Scrap Rate
The precision and automation inherent in silicone injection molding significantly lower the scrap rate compared to traditional methods. The process minimizes issues related to underfilling or overfilling molds, which can cause defects. This reduction in waste enhances overall product quality and improves production yield.
6. Automation and Scalability
The silicone injection molding process is highly automated, offering significant advantages for large-scale manufacturing. Automation boosts production efficiency and minimizes human error, ensuring consistent product quality. Additionally, automated systems can be swiftly adjusted to accommodate varying production volumes, providing a flexible solution for diverse manufacturing requirements.
Why Choose Us for Your Silicone Injection Molding
1. Enhanced Automation Efficiency
Our advanced silicone injection molding technology significantly boosts production efficiency compared to traditional methods. With a higher degree of automation, we drastically reduce production times and enable large-scale manufacturing, optimizing both speed and cost.
2. Superior Precision
Our liquid silicone injection molding process achieves exceptional precision for complex-shaped components. This high level of accuracy effectively minimizes defects such as flash, ensuring that every product meets stringent quality standards.
3. High-Security Closed System
We utilize a high-security closed system that minimizes material waste and reduces the risk of environmental contamination. This feature is especially crucial in industries like medical devices and food-grade products, where safety and cleanliness are paramount.
4. Cost-Effective Long-Term Solutions
Our flexible approach allows us to continuously optimize the injection molding process to meet various needs. We provide cost-effective solutions that ensure long-term value, particularly for high-demand applications such as medical-grade silicone components.
5. Customization Capabilities
We offer extensive customization options to tailor the silicone injection molding process to your specific requirements. From design modifications to material specifications, our solutions are adaptable to a wide range of applications.
6. Expertise and Support
Our team of experienced professionals is dedicated to delivering high-quality results and exceptional support throughout the molding process. We collaborate closely with you to address any challenges and ensure that your project is executed smoothly and efficiently.
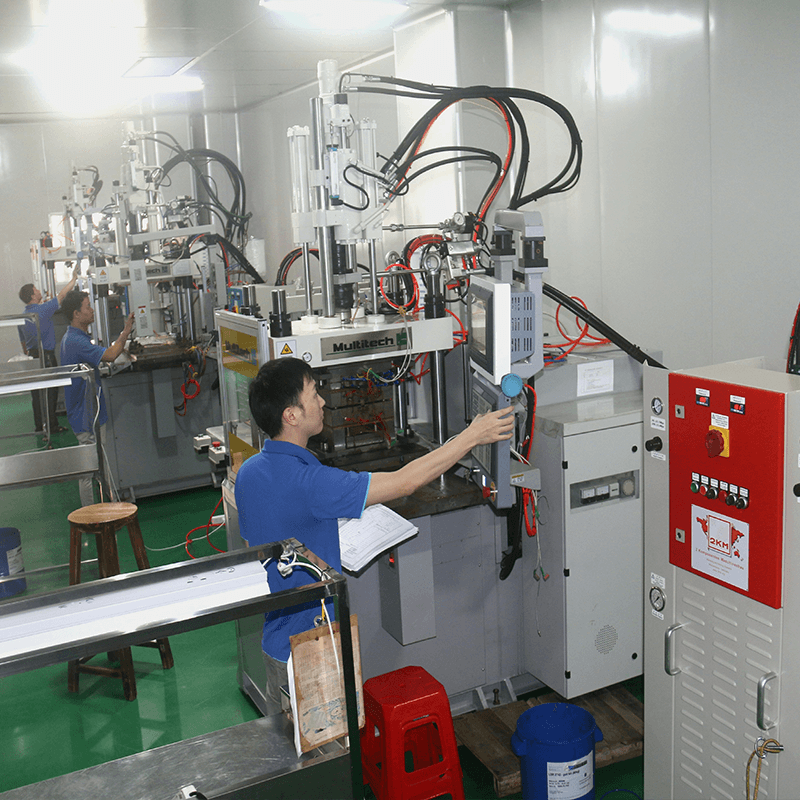
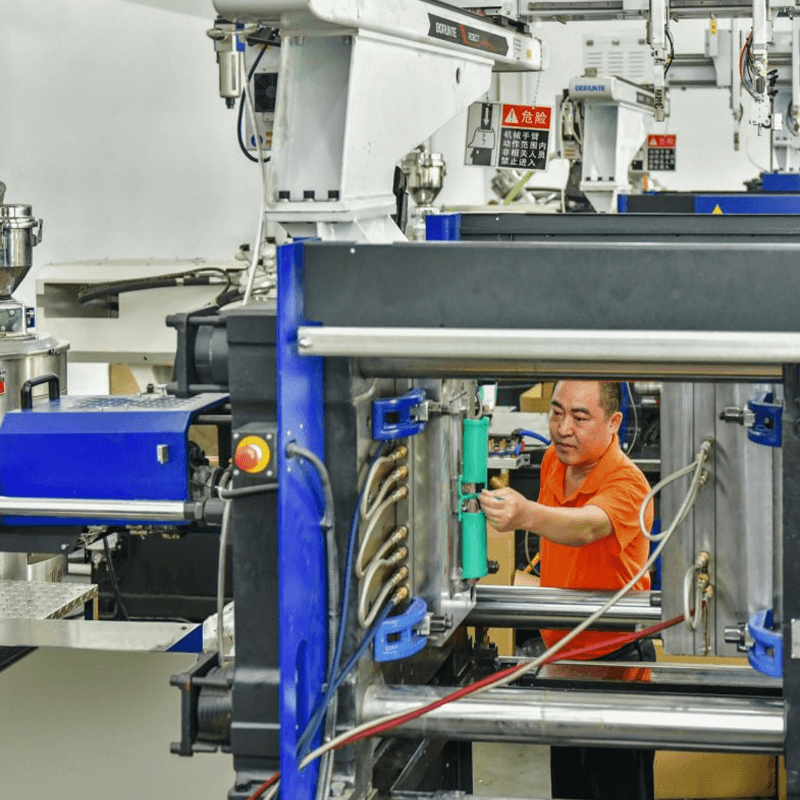
The Applications of Silicone Injection Molding
1. Medical Devices
Silicone injection molding is extensively used in the medical industry to produce high-precision components such as surgical instruments, medical seals, and wearable devices. The process is ideal for creating parts that meet stringent regulatory standards for safety and performance.
2. Consumer Electronics
In the consumer electronics sector, silicone injection molding is employed to manufacture durable and flexible components like keypads, seals, and gaskets. The high level of detail and precision achieved helps ensure reliable performance in various electronic devices.
3. Automotive Parts
The automotive industry benefits from silicone injection molding for producing high-performance parts including seals, gaskets, and vibration dampers. The process allows for the creation of components that withstand extreme temperatures and harsh conditions.
4. Food-Grade Products
Silicone injection molding is widely used to produce food-grade products such as baking molds, kitchen utensils, and seals. The process ensures that components are made from materials compliant with food safety regulations, offering both functionality and safety.
Colosilicone Silicone Injection Molding Services
Since 1998, Colosilicone has been at the forefront of delivering high-quality medical silicone components, leveraging our extensive expertise with a wide range of silicone materials and their properties.
Our advanced manufacturing facility in China is equipped with multiple high-precision horizontal injection molding machines and operates within a certified Class 10,000/ISO Class 7 cleanroom environment. This ensures that every part is produced under stringent cleanliness standards.
What sets Colosilicone apart from other silicone molding manufacturers is our highly skilled and agile production team. Custom LSR (Liquid Silicone Rubber) injection molding is our core focus, and we are dedicated to providing optimal solutions and dependable products tailored to our customers' specific needs.
Our commitment to precision and quality is unwavering. Through years of refinement, we have implemented a rigorous quality management system that meticulously tests and evaluates product quality at every stage of production.
For a competitive quote and to discuss your silicone injection molding needs, contact Colosilicone today.