About Plastic Injection Molding
Plastic injection molding is a highly adaptable manufacturing technique that involves the high-pressure injection of molten plastic into a precisely engineered mold cavity. This process is ideal for producing a diverse array of complex and durable plastic components. It is particularly well-suited for high-volume production of standardized parts, offering exceptional mechanical properties and consistency.
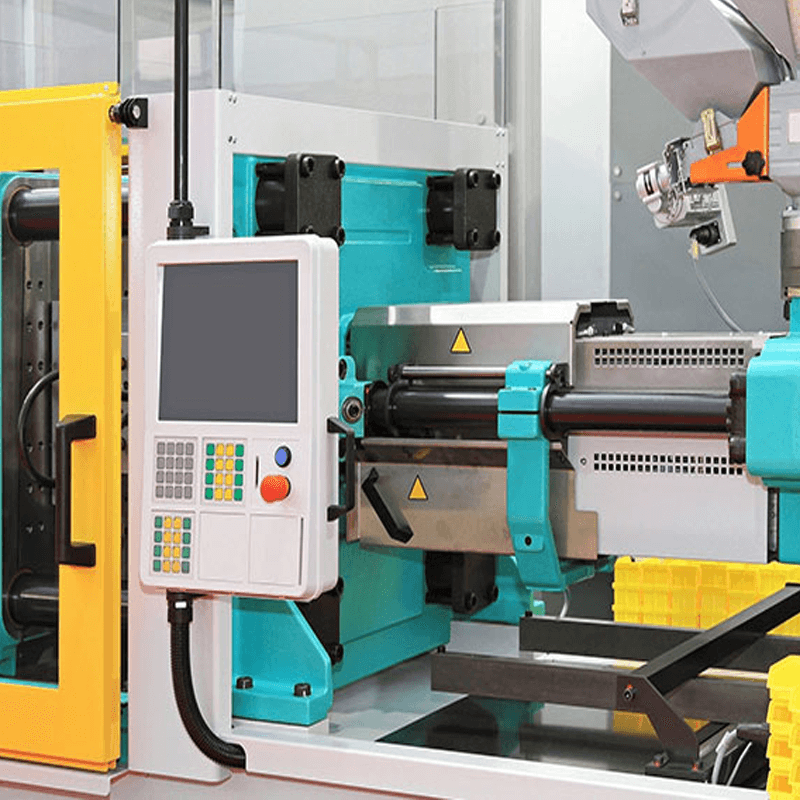
How Does Plastic Injection Molding Work
The plastic injection molding process involves several intricate steps to ensure the production of high-quality parts. Initially, we provide extensive manufacturability feedback and consultative design services to preemptively address potential mold design issues before resin is introduced. This proactive approach helps avoid common pitfalls and optimizes the mold design for better outcomes.
Once the design is finalized, our production process is meticulously documented and refined using scientific molding principles to ensure consistent, reliable results for each production run. Critical-to-quality (CTQ) dimensions specified in your models guide us in focusing on the most vital aspects of your parts’ success.
During the molding phase, parts are produced using aluminum molds, which do not include heating or cooling lines, leading to slightly longer cycle times. Our molders independently adjust and monitor fill speed, hold pressure, and hold time, while periodically inspecting part quality and aesthetics. We employ automated inline Coordinate Measuring Machine (CMM) technology to verify dimensional accuracy and generate detailed process capability studies and First Article Inspection (FAI) reports without extending lead times.
In the process, resin pellets are loaded into a heated barrel where they are melted and compressed. The molten resin is then injected into the mold’s runner system and subsequently into the mold cavity through the gates. Ejector pins are used to remove the finished part from the mold, which then falls into a collection bin. Completed parts, including the initial sample run, are boxed and prepared for shipment promptly after production.
Quality Inspections and Finishing Options for Custom Molded Parts
For custom molded parts, we offer a range of quality inspections and finishing options tailored to meet your specific application requirements. When requesting an injection molding quote, you can choose from the following services:
Quality Inspections Available for On-Demand Manufacturing Orders:
- Design for Manufacturability Feedback (DFM): Comprehensive analysis and feedback to optimize design for efficient manufacturing.
- Scientific Molding Process Development Report: Detailed documentation of the scientific molding process to ensure precision and consistency.
- In-Process CMM Inspection and Machine Monitoring: Real-time measurement and monitoring during production to maintain quality standards.
- First Article Inspection (FAI) and Process Capability Report with GD&T: Evaluation of initial parts and process capability with Geometric Dimensioning and Tolerancing (GD&T) for accuracy and performance.
Post-Processing Options:
- Mold Texturing (Mold Tech Surface Finishes): Application of surface textures to enhance the aesthetic and functional qualities of molded parts.
- Threaded Inserts: Integration of inserts to facilitate secure assembly and functionality.
- Pad Printing: Custom printing for logos or markings on parts.
- Laser Engraving: Precision engraving for detailed and durable markings.
- Component Assembly: Assembly of molded components into final products or subassemblies.
These options allow for a high level of customization and quality control, ensuring that your parts meet the exact specifications and standards required for your application.
Why Choose Us for Your Plastic Injection Molding Needs
Rapid Turnaround:
We provide exceptionally fast mold lead times, with rapid tooling available in as few as 10 business days and production tooling completed in up to 20 days.
Serial Production:
Our services are ideal for production runs starting from as few as 100 parts, ensuring flexibility for both small and large-scale projects.
Precision:
We adhere to stringent tolerance standards in line with ISO 16742, offering precision with tolerances up to ±0.07 mm, depending on the mold's accuracy and part size.
Tooling Options:
We offer a variety of tooling options, including single, multi-cavity, and family molds, to suit your specific production requirements.
Material Selection:
Our extensive selection of materials allows you to achieve the desired strength and surface quality for your parts, ensuring optimal performance.
Quality Control:
Our dedicated QA department enforces rigorous quality assurance protocols, ensuring that every part meets the highest standards of precision and reliability.
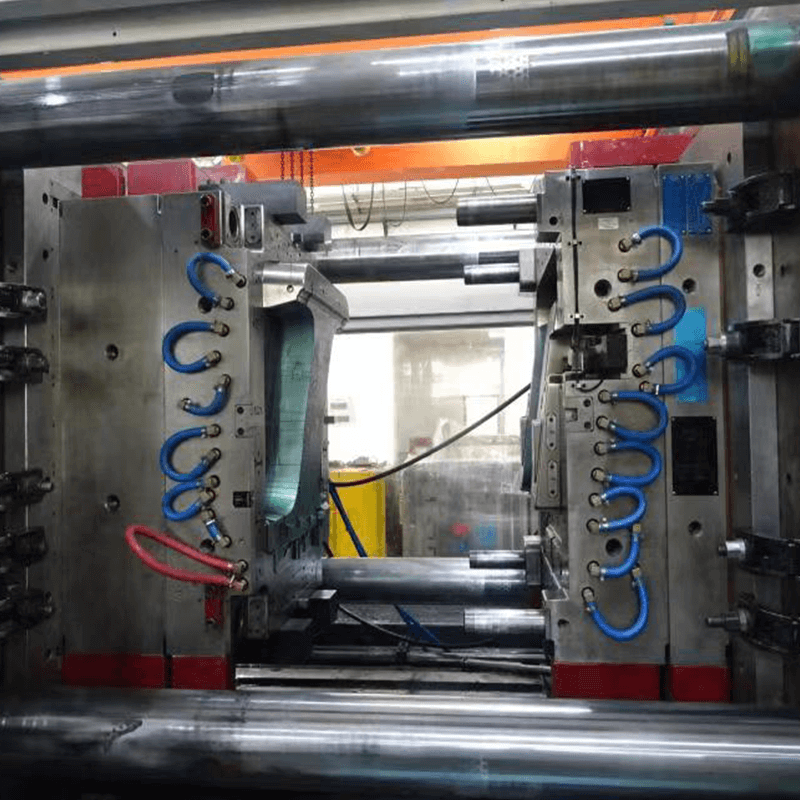
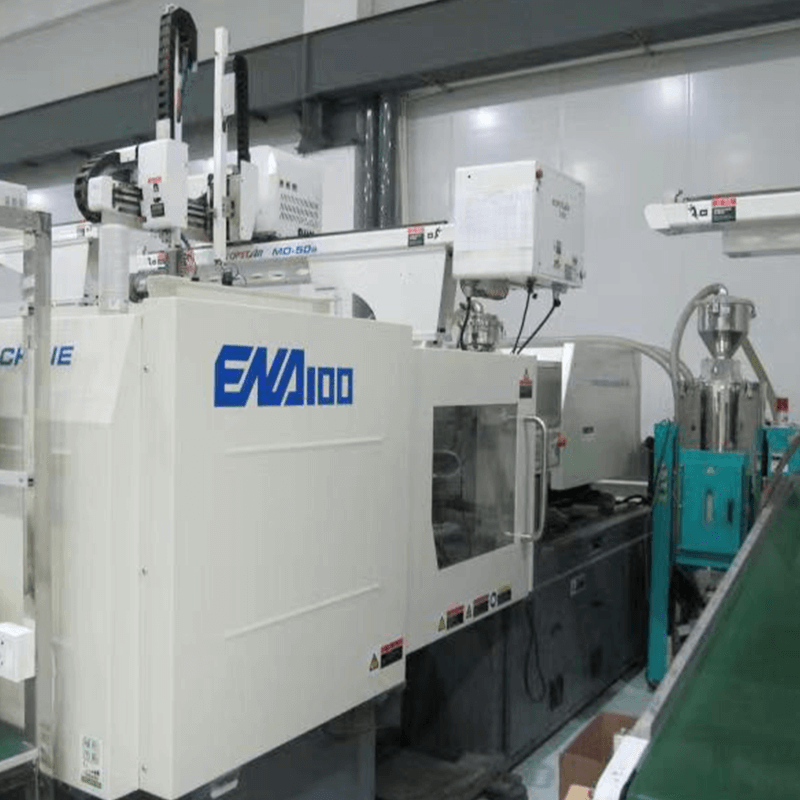
Injection Moulding Mould Classes
Mould class | Cycles | Production level | Mould base | Minimum hardness (BHN) | Description |
101 | >1 million | High | Heat-treated stainless steel | 280 | Fast cycle times and very high production rate |
102 | <1 million | Medium-High | Heat-treated tool steel | 280 | Good for parts with abrasive materials and tight tolerances |
103 | <50,000 | Medium | P20 Steel | 165 | Widely used for low to medium production parts |
104 | <10,000 | Low | Mild steel, aluminium, or alloys | <165 | Good for limited-production parts especially with non-abrasive materials |
105 | <500 | Very low | Soft aluminum, epoxy, cast materials | <165 | Mostly used for prototype production |
Our Process for Working with You on Plastic Injection Molding Projects
1. Request Manufacturing
Begin by uploading your design files. Select your desired quantity, material, and color options.
2. Quotation & DFM Analysis
We conduct a thorough design-for-manufacturability (DFM) analysis and provide you with a detailed quote within 48 hours.
3. Tool Manufacturing
Upon approval of the mold design, we proceed with the manufacturing of your custom tool.
4. Sample Production
We create sample parts, carry out comprehensive quality assurance checks, and send the samples to you for review.
5. Full-Scale Production
Once you approve the samples, we initiate the large-scale production of your parts.
6. Delivery
Your completed parts are carefully packaged and shipped to you, ensuring timely delivery and quality satisfaction.
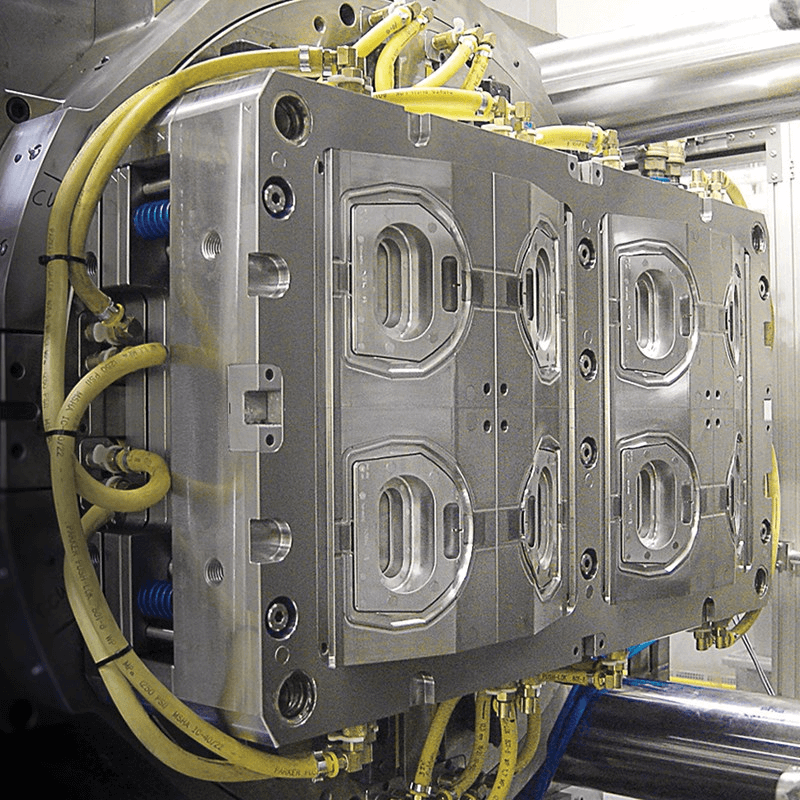
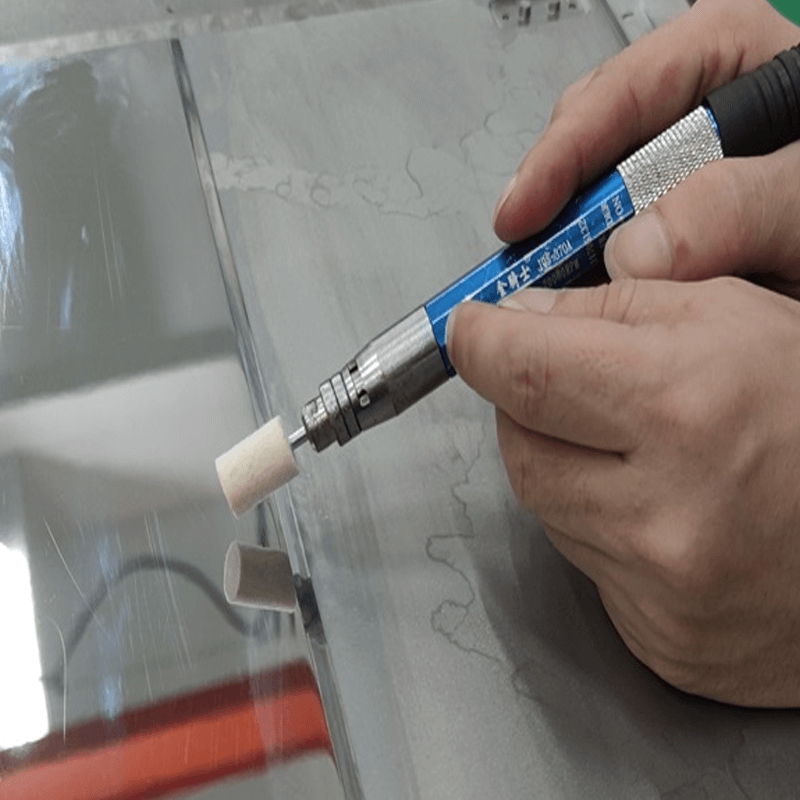
Applications
1. Automotive Industry: Producing durable and precise components like dashboards, bumpers, and interior panels, plastic injection molding is integral to automotive manufacturing, ensuring consistency and high performance.
2. Consumer Electronics: This industry relies heavily on injection molding for creating complex housings, connectors, and various components that are essential for the functionality and design of electronic devices.
3. Medical Devices: Injection molding is crucial for producing sterile, high-precision parts used in medical equipment and devices, such as syringes, implantable components, and surgical instruments, where safety and accuracy are paramount.
4. Packaging: The packaging industry utilizes injection molding to create a wide array of containers, caps, and closures that are both functional and cost-effective, ensuring products are securely sealed and protected.