Value-Added Secondary Processes
At Colosilicone, we provide integrated post-molding secondary processes designed to streamline production and enhance value. These in-line services eliminate the need for separate secondary operations, thereby boosting efficiency and productivity for our clients.
Our secondary processes are fully automated and conducted immediately after components are robotically ejected from their molds, ensuring seamless integration and optimized workflow.

Advantages & Benefits of Colosilicone Secondary Operations
1. Comprehensive Secondary Operations: We offer a full range of secondary operation services for silicone products, ensuring all your post-molding needs are met.
2. In-House Equipment and Facilities: Our advanced in-house equipment and facilities guarantee top quality, cost efficiency, and reliable delivery.
3. Expert Technical Consultation: Our specialized engineers provide expert technical consultation to optimize your silicone product designs and manufacturing processes.
4. Industry Experience: With decades of experience in the silicone products industry, we bring a wealth of knowledge to every project.
5. Reliable Delivery: We ensure stable and timely delivery of all components, maintaining consistency and reliability throughout the production process.
6. Enhanced Product Performance: By integrating our secondary operations, we improve the overall performance and functionality of your silicone products, delivering superior results.
Colosilicone Secondary Operation Services
Often, molded or extruded silicone rubber products require additional processing to achieve the final product specifications. Colosilicone excels in providing comprehensive secondary operations to deliver the exact end product our customers need.
Our secondary operations are performed in dedicated facilities by a skilled and professional team within our Secondary Operations Department. We uphold the same rigorous standards of workmanship and quality control as applied during the molding process, ensuring consistent excellence across all stages of production.
1. Post-Curing: We perform post-curing to ensure optimal material properties and durability of silicone products. This process involves additional heat treatment to complete the curing process and enhance the final product's mechanical and thermal performance.
2. Printing: Our advanced printing services include various methods such as pad printing and screen printing to apply logos, text, or other designs onto silicone surfaces, ensuring clear and durable markings.
3. Punching: We utilize precision punching techniques to create accurate holes or cutouts in silicone products. This process is essential for components requiring exact dimensions and uniformity.
4. Silk Screening: Our silk screening capabilities allow for high-quality, detailed graphics and text to be applied to silicone products. This technique provides vibrant and long-lasting prints for both functional and aesthetic purposes.
5. Slitting: We offer slitting services to cut silicone sheets or rolls into precise widths. This is crucial for producing specific dimensions and ensuring consistent material usage in downstream processes.
6. Trimming: Our trimming services involve the removal of excess material from molded silicone parts to achieve the desired shape and finish. This process ensures that the final product meets exact specifications and quality standards.
7. Cutting: We provide cutting services to shape silicone products to required dimensions, using advanced cutting equipment for accurate and clean results.
8. Bonding: Our bonding services include adhesive application and curing to join silicone components together, ensuring strong and reliable connections for complex assemblies.
9. Dipping: We offer dipping processes to apply protective or functional coatings to silicone products, enhancing their properties such as abrasion resistance or color.
10. Drilling: Precision drilling services are available to create exact holes in silicone components, which is essential for assembly or functional integration.
11. Functional Testing: Comprehensive functional testing is conducted to verify that silicone products meet performance specifications and regulatory standards, ensuring reliability and safety in their intended applications.
12. Laser Marking: Our laser marking services provide precise and permanent markings on silicone products. This method is ideal for serial numbers, barcodes, or intricate designs that require high durability and clarity.
Each of these secondary operations is carried out in dedicated facilities by our expert team, maintaining the highest standards of quality and efficiency throughout the process.
Color Matching: Silicone vs. Plastic
At Colosilicone, we offer precise color matching services for silicone products across a wide range of hardness levels, from 10 durometer to 80 durometer. Our capability to request and incorporate pigment samples of any Pantone color ensures that we can achieve the exact color specifications required for your silicone applications.
Color matching for plastic, however, presents a different set of challenges. Unlike silicone, where pigments can be seamlessly integrated across various hardness levels, plastic requires different pigment formulations depending on the type of plastic used. This complexity arises because pigments are not universally compatible with all plastic materials, necessitating careful selection and application by experienced manufacturers.
Our expertise in color matching for silicone ensures consistency and accuracy, while our knowledge of the complexities involved in plastic color matching allows us to address the specific requirements of each plastic type.
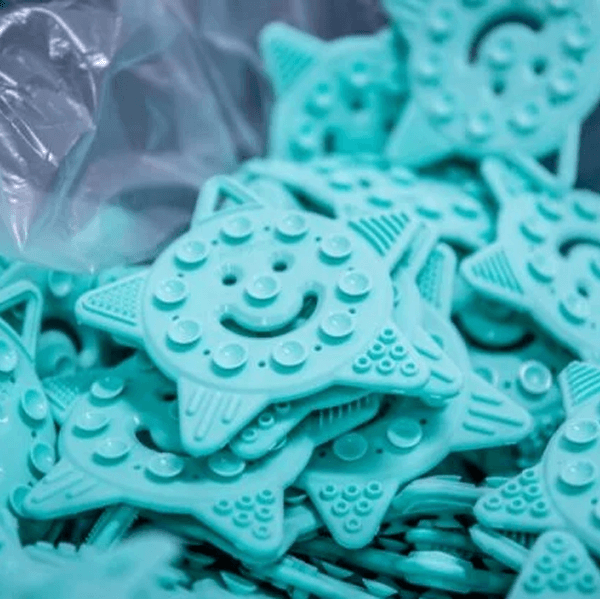
Color Matching for Silicone and Plastic Products
Pantone Matching: Pantone colors serve as the universal standard for color communication, with each color assigned a unique numerical code. At Colosilicone, we utilize this system to ensure precise color matching for silicone products. Pantone’s extensive catalog, available online and through their color guides, allows us to match your desired shade accurately.
Physical Matching: For accurate color reproduction, we can match physical items to specific pigments. Whether it’s a crayon, paint swatch, or plastic toy, our team can replicate the color of the item in silicone or plastic. Simply provide the physical sample to us or send it to our local pigment supplier for precise color matching.
FDA Compliance: When it comes to FDA compliance, the pigments used in silicone products must be safe for food contact and other sensitive applications, such as baby toys. At Colosilicone, we are experienced in producing FDA-compliant silicone products that maintain both color integrity and safety standards. Our products are free from harmful substances like BPA, ensuring they meet stringent regulatory requirements without compromising on quality.
Contact Colosilicone to Discuss Your Project
With our commitment to design flexibility, cutting-edge technology, and unparalleled quality, Colosilicone is the ideal partner for producing your high-volume silicone products. Reach out to us today to discuss your specific project needs and discover how we can bring your vision to life.