Silicone Compression Molding
Silicone compression molding is a widely adopted manufacturing technique for producing silicone products, offering a simpler and often more cost-effective alternative to silicone injection molding. This method is particularly advantageous for specific product types and production scenarios.
In silicone compression molding, a pre-measured quantity of uncured silicone rubber is placed into a mold cavity. The mold is then closed and subjected to heat and pressure. This process causes the silicone to flow and fill the mold cavity, where it undergoes curing to take on the final shape. This technique is especially effective for manufacturing thicker and less complex silicone components.
Overall, silicone compression molding provides an efficient and economical solution for producing durable and high-quality silicone products, making it a preferred choice for various applications.
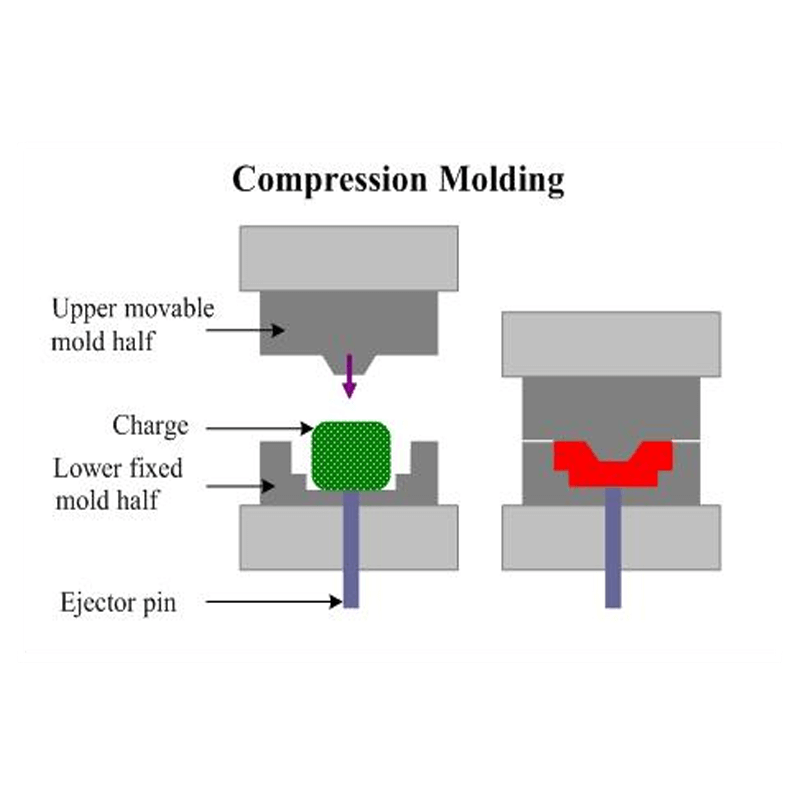
Silicone Compression Molding Process
The silicone compression molding process is a systematic method with several critical stages:
1. Material Preparation: The process starts with preparing the uncured silicone rubber, which is typically provided in sheets or blocks. The silicone is cut to the precise size and weight needed for the mold cavity.
2. Mold Design and Preparation: Compression molds are usually crafted from steel or aluminum, akin to those used in injection molding. The mold is designed with one or multiple cavities to shape the silicone into the desired form. Prior to material placement, the mold is preheated to the specified temperature to support the curing process.
3. Material Placement: A pre-measured quantity of silicone rubber is manually inserted into the mold cavity. It is crucial to use an adequate amount to fully fill the cavity while avoiding excessive flash (extra material that leaks out of the mold).
4. Compression and Curing: Once the mold is closed, pressure is applied to compress the silicone material. Heat from the mold triggers the curing process, allowing the silicone to flow and conform to the mold's shape. The material remains under heat and pressure until it is completely cured, typically taking several minutes.
5. Demolding: After the curing phase, the mold is opened, and the silicone part is removed. The component may need additional processing to eliminate any flash and refine its final properties.
6. Post-Curing (Optional): Similar to injection molding, post-curing in an oven may be employed to remove residual volatiles and enhance the material's mechanical properties. This step is especially important for parts that must adhere to specific regulatory standards.
Advantages of the Silicone Compression Molding Process
Silicone compression molding presents several advantages over silicone injection molding, making it a favorable choice in certain scenarios:
1. Cost-Effectiveness: Silicone compression molding is generally more economical than injection molding, particularly for smaller production runs. The process requires less expensive equipment and tooling, which contributes to lower overall production costs.
2. Flexibility: This method is highly adaptable, especially suited for producing thicker parts and simpler designs. It offers greater flexibility for applications where high complexity and intricate details are not required.
3. Suitable for Lower Volumes: Compression molding is ideal for applications with lower production volumes where the higher setup costs of injection molding are not justifiable. It provides a practical solution for smaller batch sizes without compromising on quality.
4. Simplicity: While silicone compression molding may not achieve the same level of precision and speed as injection molding, it excels in producing high-quality silicone parts where extreme precision is less critical. This makes it a practical alternative when manufacturing needs do not necessitate the advanced capabilities of injection molding.
In summary, silicone compression molding offers a cost-effective and flexible approach for producing high-quality silicone products, particularly in situations where complex design and high precision are not primary requirements.
Why Choose Us for Your Silicone Compression Molding Need
The Ideal Process for Prototyping
Silicone compression molding is particularly well-suited for prototyping. Single-cavity molds allow for flexible modifications, making it an excellent choice for testing and refining silicone product designs.
Enhanced Quality Control
As a well-established and mature process, silicone compression molding has a streamlined workflow compared to injection molding, potentially leading to fewer production and quality issues.
Cost-Effective Manufacturing
This process offers a more affordable alternative, especially for small businesses, helping you accelerate your project’s early stages without compromising quality.
Capability for Complex Parts
With advanced Finite Element Analysis (FEA) and high-precision mold manufacturing, silicone compression molding can successfully produce complex silicone products.
The Key Applications of Silicone Compression Molding
1. Automotive Components
Silicone compression molding is widely used in the automotive industry for producing durable and heat-resistant silicone products. These include gaskets, seals, and vibration dampers, which must withstand extreme temperatures and harsh environments while maintaining their integrity.
2. Medical Devices and Equipment
This process is ideal for manufacturing silicone products used in medical applications, such as seals, gaskets, and silicone rubber parts for medical devices. The biocompatibility and flexibility of silicone make it an excellent material for components that require stringent health and safety standards.
3. Consumer Goods
Silicone compression molding is commonly employed to produce a variety of consumer products, such as kitchenware, baby products, and electronic accessories. The process allows for the creation of high-quality silicone products that are safe for everyday use and comply with food-grade and safety regulations.
4. Industrial Applications
In industrial settings, silicone compression molding is utilized to manufacture silicone products like custom gaskets, seals, and insulation components. These parts are crucial in environments that demand high resistance to chemicals, temperature extremes, and mechanical stress.
Tailored Silicone Compression Molding Solutions for Your Business
We align with your timelines and budget to deliver exceptional silicone products. Specializing exclusively in the manufacturing of molded silicone rubber components, we have perfected the production of high-quality compression-molded products. Our company elevates "custom" to new heights with our Silicone Compression Molding Solutions™. As a leading manufacturer of Liquid Silicone Rubber parts, we've served some of the world's largest corporations. Our advanced capabilities cover every aspect of design and production, offering part design support to optimize manufacturability (DFM) and performance. We provide premium-quality tooling, high-volume production, and packaging solutions to keep your overhead costs low. Contact us today for a personalized quote.