Our Silicone Overmolding
Silicone overmolding is an advanced manufacturing process where silicone rubber is molded over a pre-formed substrate, such as plastic or metal, to create a unified component. This technique combines the superior properties of silicone, including flexibility, durability, and chemical resistance, with the structural strength of the underlying material. By injecting liquid silicone rubber (LSR) over the substrate under high pressure, the two materials bond seamlessly, resulting in a high-performance part ideal for applications across consumer electronics, medical devices, automotive components, and industrial uses. Silicone overmolding is prized for its ability to produce complex shapes and enhance product functionality while maintaining exceptional quality and consistency.
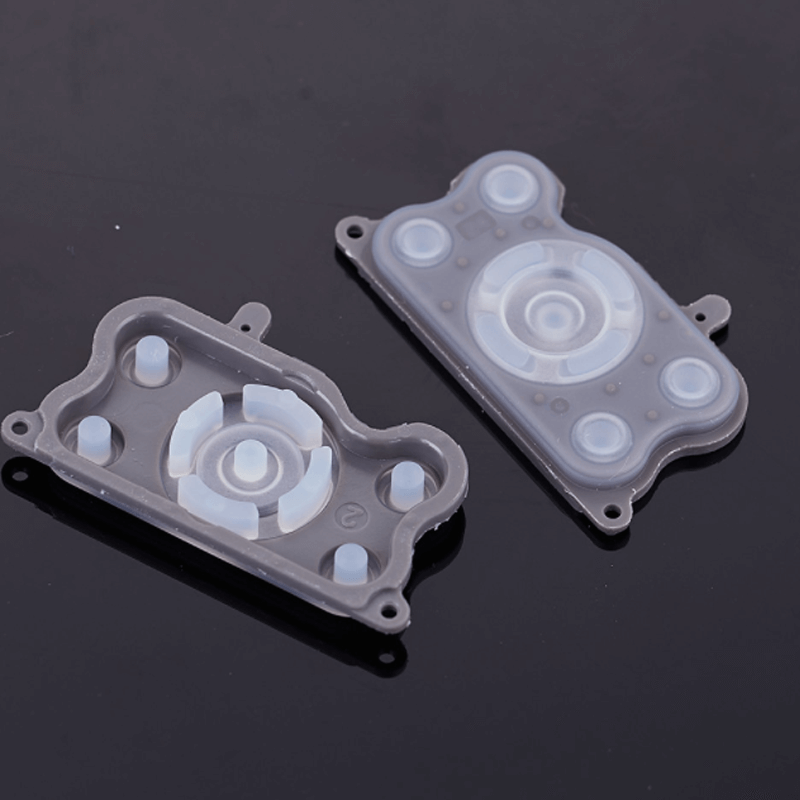
Advantages of Silicone Overmolding
1. Integrated Functionality: Overmolding liquid silicone rubber (LSR) onto a pre-formed thermoplastic substrate within the same mold and machine allows for the integration of materials and functions into a single component. This results in a seamless fusion of parts, enhancing the overall performance and cohesion of the final product.
2. Enhanced Material Properties: By combining LSR with thermoplastics, you leverage the best properties of both materials. This integration provides superior flexibility, durability, and chemical resistance, while also eliminating the need for additional post-molding assembly operations.
3. Cost Efficiency: The use of a single tool and machine cycle for the entire process reduces initial investment and tooling costs. This efficiency also lowers the cost of inspection and qualification, making it a cost-effective solution for high-quality production.
4. Improved Production Efficiency: The single-cycle nature of the overmolding process streamlines production, allowing for faster turnaround times and higher quality control. This efficiency ensures a more consistent and reliable manufacturing experience.
5. Wide Application Range: The ability to combine various materials through overmolding opens up new application areas that may be challenging to address with traditional silicone molding methods. This versatility expands the potential use of silicone parts in various industries.
6. Design Flexibility: Silicone overmolding offers enhanced design possibilities, enabling products to achieve advanced properties such as superior waterproofing, compression resistance, and sealing. This flexibility allows for innovative and customized solutions tailored to specific application requirements.
Silicone Overmolding Production Process
Silicone overmolding involves a multi-step process where silicone is applied to a pre-formed substrate to create a unified component. The bond between the silicone overmold and the substrate is achieved through either chemical adhesion or mechanical interlocking features. Mechanical undercuts, protrusions, or indentations are used to enhance the bond and prevent the silicone from detaching from the substrate.
Molding Steps:
1. Substrate Placement: Position the pre-formed thermoplastic part, metal component, or other specialty substrate into the mold cavity. Alternatively, inject the raw thermoplastic material if starting with an unformed substrate.
2. Injection of LSR: Close the mold and proceed to inject liquid silicone rubber (LSR) into the mold cavity. If the substrate was initially injected, rotate the mold to facilitate the LSR injection process.
3. Filling and Coverage: Ensure that the LSR completely fills the mold cavity and thoroughly covers the substrate.
4. Completion: Finalize the molding process, allowing the silicone to cure and solidify, creating a robust bond between the silicone and the substrate.
Substrates for Silicone Overmolding
Silicone overmolding offers considerable flexibility in substrate selection, allowing for the integration of various substrates, either identical or different, to achieve the desired product characteristics.
Common substrates used in silicone overmolding include non-toxic thermoplastics and metals. Incorporating these substrates allows for modifications in the appearance and hardness of the silicone product, while enhancing functionality such as waterproofing, insulation, shock resistance, and sealing. This versatility adds significant value to product design.
When considering silicone overmolding, insert molding is a specific process that involves embedding the substrate within the silicone mold. Metal is often the preferred choice for insert molding due to its high-temperature resistance and enhanced hardness.
For certain material combinations, it may be necessary to prepare the substrate through processes like firing, discharge, or plasma treatment. Additionally, it is crucial to test the adhesion between the substrate and the liquid silicone rubber (LSR) to ensure optimal performance and make necessary adjustments to the production process.
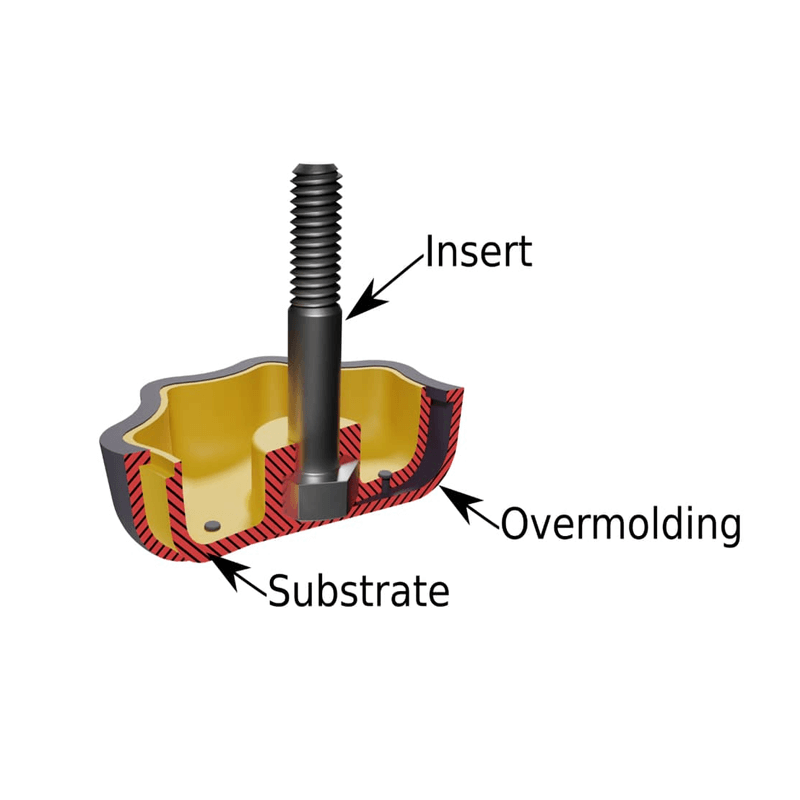
When is Overmolding Used?
Overmolding is employed in various scenarios where the enhancement of a product's functionality, durability, or aesthetic appeal is required. This manufacturing technique is particularly useful when integrating multiple materials or achieving specific performance characteristics within a single component. Here are the primary industries where overmolding is commonly utilized:
1. Medical Devices: Overmolding is frequently used in medical device manufacturing to improve grip, provide cushioning, and enhance durability. This technique allows for the creation of components with complex geometries and multi-material constructions, which are essential for medical tools, diagnostic equipment, and surgical instruments.
2. Consumer Electronics: In the consumer electronics sector, overmolding is employed to combine functional and aesthetic features, such as adding soft-touch surfaces to devices and enhancing ergonomics. It is commonly used in the production of smartphone cases, remote controls, and wearables, where both protection and user comfort are paramount.
3. Automotive Industry: Overmolding is applied in automotive manufacturing to produce parts that require both strength and flexibility. This includes components like seals, gaskets, and trim parts, which benefit from the enhanced performance characteristics of overmolded materials, such as improved sealing and noise reduction.
4. Industrial Equipment: In industrial applications, overmolding is used to create durable and high-performance components that can withstand harsh environments. This includes parts such as grips, handles, and protective covers, which need to endure mechanical stress, temperature variations, and chemical exposure.
Overall, overmolding provides a versatile solution for enhancing product functionality, improving user experience, and extending the lifespan of components across these diverse industries.
As a leading authority in the custom silicone rubber industry, Colosilicone has been delivering top-tier LSR overmolding solutions to clients worldwide for many years. Our extensive experience in the field, particularly in producing medical-grade components, underscores our commitment to excellence.
Colosilicone offers a comprehensive suite of services for LSR overmolding, including custom design consultation, material performance testing, high-volume production, and rigorous quality assurance. Our team of experts is available to provide personalized advice and support, ensuring that all your project needs are met with precision and efficiency. Contact us today for a consultation.