Two-Shot Injection Molding
Two-shot injection molding, also known as "2k molding" or co-injection molding, is an advanced process that requires a specialized co-injection molding machine. This process is particularly important in the production of silicone products, where precision and accuracy are paramount. The method involves molding liquid silicone rubber (LSR) and a secondary material, either a compatible thermoplastic or a different grade of LSR with varying durometers or pigments, in a single molding cycle. The expertise of skilled mold builders and LSR processors ensures that the materials are precisely aligned and accurately placed. As a result, two distinct materials are seamlessly integrated into one cohesive component through this sophisticated two-shot injection molding process.
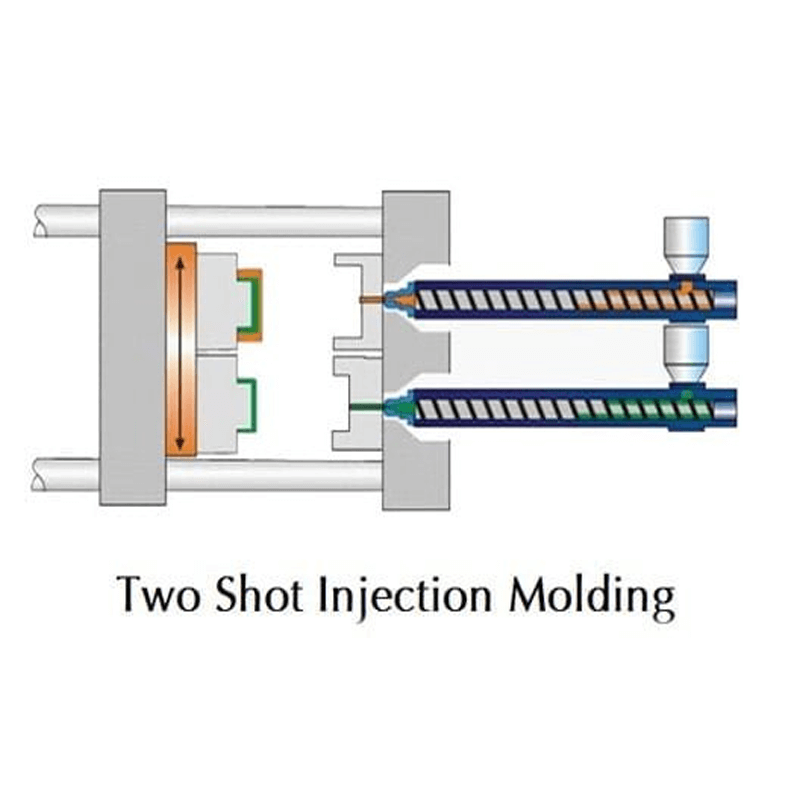
2-Shot vs. Overmolding: What's the Difference
While two-shot molding and overmolding are often confused due to their similar end results—both involve combining two different materials—their processes and bonding characteristics differ significantly. In the context of silicone products, two-shot molding, also known as 2k molding, involves the simultaneous injection of two materials. These materials are chemically and physically bonded during the molding process, resulting in a superior and seamless integration of the materials.
On the other hand, overmolding involves placing a pre-molded component or a metal substrate into the LSR mold. The liquid silicone rubber is then molded around or over this substrate, creating a physical bond. Although overmolding effectively integrates two materials, the bond achieved is typically not as robust as that of the two-shot molding process. This distinction is particularly crucial when producing silicone products that require enhanced durability and precision.
The Advantages of Two Shot LSR Molding
Cost and Time Efficiency
When designing silicone products with multiple components, each with specific features and functions, integrating these elements into a single manufacturing process can lead to substantial cost and time savings. By reducing the need for additional assembly steps or secondary operations, you save on production costs, manual labor, and material handling. This streamlined approach significantly reduces production time, making it an efficient and economical solution.
Enhanced Efficiency and Quality
The integration of fewer production steps and a seamless material transition results in a more efficient manufacturing process for silicone products. By minimizing the number of operations and relying on fewer suppliers, the supply chain is streamlined, reducing the risk of errors and enhancing overall product quality. This method ensures that the final product meets stringent quality standards with greater reliability.
Design Optimization
LSR multi-shot technology enables the optimization of part weight, space, and complexity, allowing for the integration of multiple materials and functions into a single component. This process is ideal for producing silicone products with tight tolerances, consistent wall thickness, and intricate geometries. In some cases, complex designs that require the use of dual materials can only be realized through a two-shot injection molding process.
Proven Expertise in Complex Solutions
At Colosilicone, we have mastered the art of multi-shot LSR injection molding, making us one of the few providers capable of delivering the precision and quality needed for intricate and critical silicone products. Our expertise allows us to consistently produce high-quality, multi-material components that meet the demanding performance requirements of long-term, high-volume programs. We take pride in offering our customers innovative solutions that ensure their products perform reliably over time.
Two-Shot Injection Molding Process
Two-shot injection molding utilizes two distinct injection phases within a single cycle, unlike traditional single-shot injection molding. This process employs a specialized mold designed to accommodate both injections without removing the partially finished part between shots.
Initially, the mold is closed to form the first cavity. During this phase, the runner for the second shot is sealed off, while the runner for the first material is aligned with the base material's sprue. The first material is then injected to fill the cavity.
Two-Shot Terminology
Term | Definition |
Boss | A raised feature on a part designed to aid alignment during assembly or attachment to other components. |
Cold-Runner Mold | A mold where the runners are maintained at the same temperature as the mold and are ejected at the end of each cycle. |
Draft | A slight taper on the mold walls to facilitate the removal of the part from the mold. |
Flash | Excess material that forms along the seams or parting lines of the mold cavity. |
Gate | The channel through which molten plastic enters the mold cavity. |
Runner | A channel within the mold that directs molten resin from the machine sprue to the cavity gate. |
Short Shot | Incomplete filling of the mold with resin, resulting in missing geometry and melted edges. |
Shrinkage | The reduction in size of a plastic part as it cools. |
Shut-Off | An area where the mold seals against another mold half, insert, or substrate to create a slot, hole, or void. |
Hot-Runner Mold | A mold with insulated or heated runners to maintain resin in a molten state for better flow control. |
Knockout Pin | A pin used to eject the molded part from the mold. |
Living Hinge | A thin, flexible section of a part allowing it to fold. |
Parting Line | A mark on the molded part where the two halves of the mold meet. |
Rib | A thin, wall-like feature that enhances the bending stiffness of wall sections and bosses. |
Sink Mark | An indentation on the surface caused by uneven cooling in areas with significant changes in wall thickness. |
Sprue | The channel through which molten plastic flows from the machine nozzle to the mold runner. |
Undercut | A protrusion, hole, or recess in the part that hinders ejection from the mold, requiring movable mechanisms to form the shape. |
Applications
1. Medical Devices: This process is ideal for producing high-precision, biocompatible silicone products used in medical devices, ensuring safety and performance in critical healthcare applications.
2. Automotive Components: Two Shot LSR Molding is widely utilized in the automotive industry to manufacture durable and resilient silicone products, such as seals and gaskets, that withstand extreme conditions.
3. Consumer Electronics: The technology enables the production of complex, multi-material silicone products, such as keypads and protective casings, enhancing the functionality and durability of electronic devices.
4. Industrial Equipment: This process is used to create robust, high-performance silicone products for industrial applications, offering superior resistance to chemicals, temperature, and wear.
Leading the way in multi-injection molding innovation at colosilicon
Colosilicone stands at the forefront of multi-injection molding technology, pioneering cutting-edge solutions that seamlessly integrate multiple functions and materials. Our proprietary multi-shot molding process is a testament to our industry-leading expertise, offering unparalleled precision, quality, and versatility.
Our state-of-the-art molds and advanced molding capabilities empower us to meet even the most intricate design challenges without compromising on quality, durability, or visual appeal. Beyond our core multi-shot injection process, we provide a comprehensive suite of value-added services, including design consultation, prototyping, and integrated secondary processes, ensuring a complete and seamless experience for our customers.
Discover how Colosilicone’s multi-injection molding expertise can elevate your manufacturing processes and applications. Contact us today to explore the transformative potential of our innovative solutions.