A baby silicone feeder is a handy tool that allows babies to safely explore solid foods while reducing the risk of choking. Made from soft, flexible silicone, these feeders have small holes that allow babies to suck on and mash soft foods without the risk of large chunks getting through. The silicone feeder is a great way for babies to experience a variety of textures and flavors while promoting self-feeding skills.
Food ideas for a baby silicone feeder include small pieces of soft fruits like bananas, pears, or apples, which are easy to mash and can be placed inside the feeder for baby to enjoy. You can also try frozen purees of fruits or vegetables like peas, sweet potatoes, or carrots, which can soothe teething discomfort. Small, soft-cooked veggies like zucchini, pumpkin, or avocado can be safely placed inside, offering nutrients while encouraging chewing. For added variety, try introducing small bits of cheese or rice, keeping the foods simple, soft, and appropriate for your baby’s age and developmental stage. The silicone feeder is an ideal way to expose babies to healthy foods and encourage independent eating while ensuring safety.
Basic Information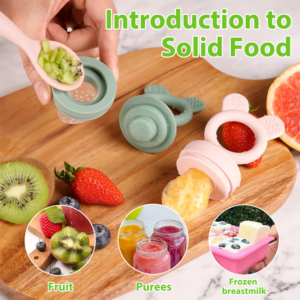
Material:100% premium food-grade silicone
Color:Can be customized
MOQ:According to your design
Dimensions:Custom Sizes
Customization and Manufacturing Process for Silicone Baby Care Products:
- Design Concept Development
– Collaborate with clients to develop and refine design concepts based on functional requirements and aesthetic preferences.
- Design for Manufacturability (DFM)
– Create detailed design blueprints and perform a DFM analysis to ensure the design is practical and cost-effective for manufacturing.
- Material Selection
– Choose high-quality, food-grade silicone and other materials that meet safety standards and durability requirements.
- Prototype Creation
– Develop prototypes using 3D printing or rapid prototyping techniques to test the design and functionality before mass production.
- Tooling and Mold Design
– Design and manufacture precision molds or tooling required for mass production, ensuring they align with the final design specifications.
- Injection Molding
– Utilize advanced silicone injection molding techniques to produce high-quality, consistent silicone parts based on the finalized molds.
- Quality Control and Testing
– Conduct rigorous quality checks and product testing to ensure compliance with safety standards and performance requirements.
- Customization and Branding
– Apply custom branding, logos, or additional features as requested by the client, including color choices and packaging designs.
- Assembly and Packaging
– Assemble finished components if necessary and package products according to client specifications, ensuring they are protected during transit.
- Final Inspection and Delivery
– Perform a final inspection of the products and coordinate delivery to ensure timely and accurate fulfillment of orders.
- After-Sales Support
– Provide ongoing support and address any post-production issues or customer inquiries to ensure complete satisfaction.
Reviews
There are no reviews yet.